Here is your most recent issue of the High Current News e-newsletter. It's packed full of information to keep you updated with the latest MIG & TIG welding news, product information and new updates from D/F MACHINE SPECIALTIES.
D/F is a world leader in the design, development, and manufacture of MIG & TIG welding products, consumables & accessories.
|
|
NEW D/F Product Catalog
D/F has released a brand new color product catalog! Featuring the most popular D/F MIG & TIG welding equipment, accessories and consumables, the catalog will cater to your informational and ordering needs.
You can request your own free copy of the catalog in two ways:
1. Email D/F at sales@dfmachinespecialties.com with your name, and your company's name and address of where you would like the catalog to be sent.
2. Fill out the reservation form located here.
Click to download the catalog as a digital PDF.
|
|
Hardfacing & Overlay Torches
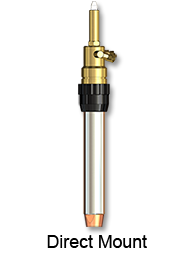 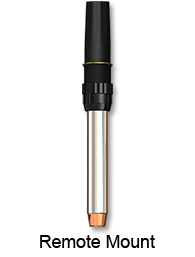
For automatic and robotic hardfacing applications, D/F recommends the MIG Water-Cooled-to-the-Tip Machine Barrels. These versitile torches will handle any hardfacing application. View these torches on the web site:
D/F Direct Mount (Automatic) Water-Cooled-to-the-Tip MIG Machine Barrels
D/F Remote Mount (Robotic) Water-Cooled-to-the-Tip MIG Machine Barrels
What is Hardfacing?
Hardfacing involves the process of layering on a tougher, stronger metal across the face of a base metal for the purpose of reconditioning a surface that undergoes much normal wear and tear demanded by the job that it is used within. Examples of these base metals might include the faces of shovel buckets, crusher plates and teeth, pipes, and extruder screws. Hardfacing is often applied to new products at the time of production to increase the life of the face from the beginning.
What Types of Demands will Hardfacing Satisfy?
Hardfacing can be used to protect agains any number of physical demands such as metal to metal wear, thermal loads, fricional and grinding wear, impact, corrosion, scaling, and many others. In some cases, more than one of these types of demands may occur simultaneously, so the weld metal must posses the respective properties. Hence, a conscientious selection of the proper weld metal will be a must. Of course, there doesn't exist a weld metal possessing all these properties in full measure. Nevertheless, in most cases it will be possible to find a satisfactory compromise in practice.
What is the Overall Benefit of Employing Hardfacing?
The initial cost and time needed to apply hardfacing to a pipe, tool, or other machine part is small compared to the time and money saved in the long run. Hardfacing will help prevent the general wear and tear associated with the work done by these tools and machines, making them last much longer, and allowing them to do much more work. Time and money are saved as the need for replacement parts and tools is kept to a minimum.
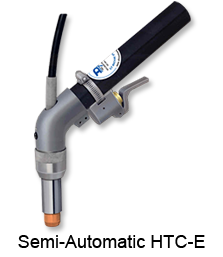 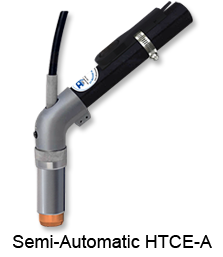
For semi-automatic hardfacing and overlay applications, D/F recommends the MIG Water-Cooled Semi-Automatic 55° Torches with External Casing. These versitile torches will handle any hardfacing application. View these torches on the web site:
D/F Water-Cooled Semi-Automatic 55° Torches with External Casing
Similar to the automatic and robotic heavy duty torches above, these semi-automatic 55 degree water-cooled torches with external casings use an axial alignment of the casing to reduce wire feed pressure and improve current tip life. The gun assembly is available with an extended handle (8"-20") and slide switch to help keep the welder away from the extreme conditions of preheat and high amperages required for overlay applications, steel casting repairs, surfacing and rebuilding applications. Because of the robust design and great success when using this torch, it can be converted form semi-automatic to automatic by easily removing the trigger switch and cable, installing a manipulator, mounting the torch on a boom, and allowing the welder to get 15' back away from the heat, thus using the trigger back by the wire feeder.
The D/F torch is famous for the fact that if it is chilled properly, the welder can grab the front of the torch with their bare hand and it will be cold to the touch seconds after welding. With the proper chiller, this can be done even after a 4 hour arc time. Make certain the cooling water supply is at least the minimum flow rate of 3 quarts per minute (for each inner body), at 40 psi (80 psi maximum) with a 5 gallon reservoir and 15,000 BTU/hr cooling capacity. D/F Machine Specialties does not manufacture or sell chillers, we only recommend them. Click here to see our recommended chillers.
If you have any questions about hardfacing, please do not hesitate to contact the factory.
Phone: (507) 625-6200 · Email: sales@dfmachinespecialties.com
We look forward to helping you with your welding applications!
|
|
Duty Cycles & Ratings
When using an arc welding machine, it is crucial to understand what its duty cycle is as it will help you preserve the life and quality of the machine. When purchasing a MIG welder it will have a specification on the packaging or in the manual called the duty cycle. This refers to the amount of welding that can be achieved in a given amount of time. The reason this specification is important is it informs the user of how long the MIG welder can work at its optimum level.
Duty cycle refers to the amount of time a welder will weld in a given time frame at given amperage. The duty cycle is a rating that indicates how long a welding machine can be used at its maximum output current without damaging it. Duty cycle is based on a ten-minute time period. A welding machine with a 60% duty cycle can be used at its maximum rated output current for six out of every ten minutes. The welding machine may overheat if the duty cycle is exceeded. At lower current settings, the duty cycle may be increased and the power source used for a longer period of time.
As an example, a welder with a 20% duty cycle means it can be used for 2 minutes out of 10 at a given amperage setting, and then it must cool down. A welder with a 50% duty cycle can be used for 5 minutes out of 10 at a given amperage. These are just guidelines, and each unit might run more or less at different levels. Most spec sheets will show how the duty cycle will scale from high to low settings. Most equipment is rated at 2/3 to 3/4 of its maximum output. When you are using less amps the duty cycle goes up, more amperage it goes down.
It is important to note that duty cycle becomes inaccurate when being measured over a different time period, especially a longer one. One welder might have a duty cycle of 50% at 200 amps, and this means it can run for 5 minutes out of 10 before it has to be shut down to cool off. It does not mean that the same welder can be run for 30 minutes out of an hour at 200 amps, even though 30 minutes is 50% of an hour just like 5 minutes is 50% of 10 minutes. Duty cycle must be consistently measured in a 10 minute time frame.
Ambient temperature and humidity can have some effect on the duty cycle. A machine will sense its temperature via a thermocouple, and will shut down when it exceeds its duty cycle, coming back on line when it has cooled. To improve or maintain duty cycle, run the machine at minimum amps required for the job, keep the fan area clean, and have the inside of the machine cleaned by a repair center or by yourself, making sure to unplug the power cord occasionally. In the event that the duty cycle is exceeded and the breaker is tripped, allow the MIG welder to cool down for at least 15 minutes. A rated duty cycle on any MIG welding machine is there to protect you and your welder from any long-lasting damage.
Torch Ratings
Since its inception, welding has been a major element in the production environment. Real production welding is 100% duty cycle welding, and if a facility is not welding 100% of the time, it is losing money. With a 60% duty cycle, who can afford to run for 6 out of 10 minutes and have 40% of their production time as down time? This is a very costly method of production, and is the reason why all D/F Machine Specialties torches are rated with 100% duty cycles. A properly water-cooled D/F torch that runs at 650 amps with a 100% duty cycle really means that it will run 3 shifts a day, 7 days a week, all year round at 650 amps with no need for cool down. No other torch will remove downtime like a D/F torch.
D/F Machine Specialties torches were designed for production welding. The core of these designs come from a time when all the big-box manufacturers were selling 1000 amp power supplies. It takes a very robust torch to withstand 1000 amps or to work above 1000 degree preheat. All D/F torches were designed on this premise and will last years upon years rather than mere months. D/F currently has thousands of torches in circulation that have been run for over 20-30 years.
Consumable Use
With downtime removed and the ability acquired to produce 100% of the time, D/F torches can promise an average increase in the life of consumables (tips and nozzles) of up to 7-to-1 times. A contact tip will not have to be changed every 40 minutes as it would with competitors' torches, but rather after an entire day or an 8 hour shift. The competitions' torches also have 3/4" long contact tips. The average D/F tip is 2.5"-3.5" long. The longer tips allow D/F torches to maintain the most stable arc in the industry. They provide built-in wire straightening and consist of more copper which translates to more heat dissipation. With the built-in wire straightening and longer tip, the wire comes out straight and does not wander or prematurely wear out the contact tip as it does with the competitors' 3/4" long tips. The new series of Automatic and Robotic Water-Cooled-to-the-Top torches by D/F Machine Specialties actually has the tip recessed 1" into the water-cooled, copper inner body, never allowing the copper tip to heat up and soften. Just ask around; D/F torches are famous for the fact that seconds after you weld, they can be grabbed with bare hands and will be cold to the touch.
If you are interested in learning more about D/F Machine Specialties heavy duty MIG water-cooled torches, or have questions about our capabilities, please contact us. We would be more than happy to discuss the product you are manufacturing and your current operations, including your required amperages, wire size and type, power source and feeder, size restrictions and limitations, etc. We cannot get every welding account out there, and we will be the first ones to tell you that we may or may not be able to help, but we would love the opportunity to discuss the ways that our torches may provide solutions that will benefit your welding applications.
At D/F Machine Specialties we have no outside salespeople. Our torch is our salesperson. We are more than happy to run a purchase-pending trial and evaluation with potential customers that we feel can benefit from using a heavy duty D/F torch. We look forward to running our torches against what a customer has been using for years. We know how hard it is to get a customer to try something new or to change. In almost all cases, the D/F torch will sell itself within 1 week.
|
|
Frequently Asked Questions
D/F has now added a Frequently Asked Questions page to the website! This page will be continually updated with information about Torch Maintenance, Welding Practice & Setup, Warranty & Refurbish, Troubleshooting, and more in hopes of fulfilling the needs of anyone who might have a common question about D/F's equipment or welding in general. Please visit the FAQ page.
|
|
Do You Have Videos or Photos of D/F Torches in Action?
Submit Them to WIN!
D/F's new Video and Photo Galleries showcase D/F equipment in action over the years, and we are constantly adding to the galleries. We want to see how our equipment helps brings out the best of your creativity and skill, or simply how your equipment is setup and used.
Submit your videos and photos to:
HighCurrentNews@DFMachine.com
For project submissions, things to include:
- Video or Photos of your project
- What did you make?
- How did you make it?
- Which D/F products did you use?
Submissions will be put in a drawing for a chance to Win A Gift Card to your local Best Buy Consumer Electronics Store.
Check out the D/F Photo Gallery here.
Check out the D/F Video Gallery here.
|
|
Words from the Editor
Greetings from D/F!
Thank you for reading our High Current News e-newsletter. Please share this issue with a friend and send us your comments.
Enjoy!
Best Regards,
D/F Machine Specialties, Inc.
|
|
|
   |
Follow D/F
   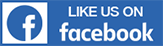
|
In This Issue
• NEW D/F Product Catalog
• Hardfacing & Overlay Torches
• Duty Cycles & Ratings
• Frequently Asked Questions
• Got Projects? Submit to WIN!
• New Products
• Nozzle Thread Chaser Taps
|
New Products - Automatic & Robotic Machine Torches
The versatile D/F curved quick-change Water-Cooled Automatic and Robotic 500 amp Torch Models NCC/LRN and HTC/LRN can be used for a wide range of automatic applications. With the various angles (22° through 90°) and lengths available, a selection may be made to suit individual requirements.
Read More
|
|
|
|
|
|
|
|
Nozzle Thread Chaser Taps
The New D/F Nozzle Thread Chaser Taps are designed to chase and tap nozzle threads to clean and repair them for better conductivity and contact.
• No need to remove the
contact tip
• Chasing will clear debris,
metal filings and spatter
• Re-tapping will straighten and
clean damaged threads
• Tap sizes available for all D/F
Nozzle Assemblies
Read More
|
Your Downloads
Did you know you can download all of D/F's Catalogs, Instruction Manuals and CAD Files at D/F's Online Download Center?
|
Contact D/F
Product Info: 1-507-625-6200
Fax: 1-507-625-6203
Online: Contact D/F
D/F Machine Specialties, Inc.
1750 Howard Drive
North Mankato, MN 56003
|
|